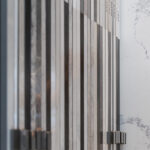
Learn about our manufacturing processes
All of our surfaces meet exacting standards of excellence from the initial procurement of raw materials to the final quality control check. Our highly skilled and trained staff ensure the quality of a product that is unrivalled in the industry today.
We manufacture Caesarstone premium quartz, mineral and porcelain worktops through a highly automated yet strictly monitored process that includes the following steps:
Caesarstone Quartz and Mineral surface manufacturing process
Our quartz and mineral manufacturing process begins with a rigorous inspection of all incoming raw materials, and blends the highest quality natural minerals with pigments and polymer resins.

1. Feeding and mixing
The raw materials (including quartz, feldspar, pigments and polymers) are carefully selected, tested, and mixed.
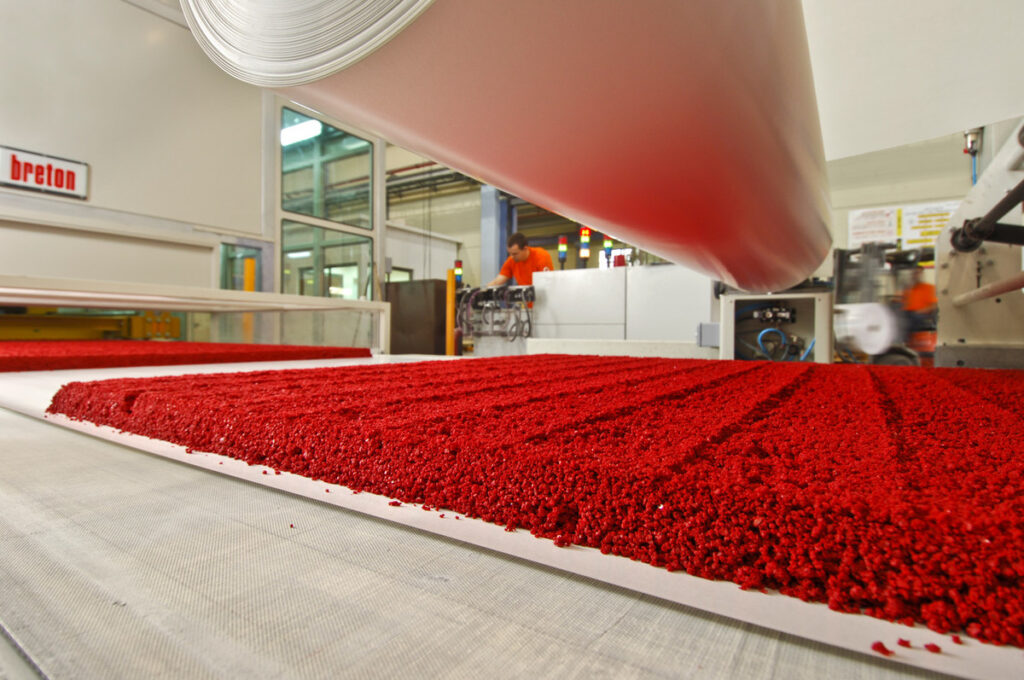
2. Moulding and pressing
The mixture is then poured into a mould and formed into large format slabs. Next, it is compressed under very high pressure (nearly 100 tons psi) and vibrated in a vacuum. This process removes all the air and creates a compressed surface.
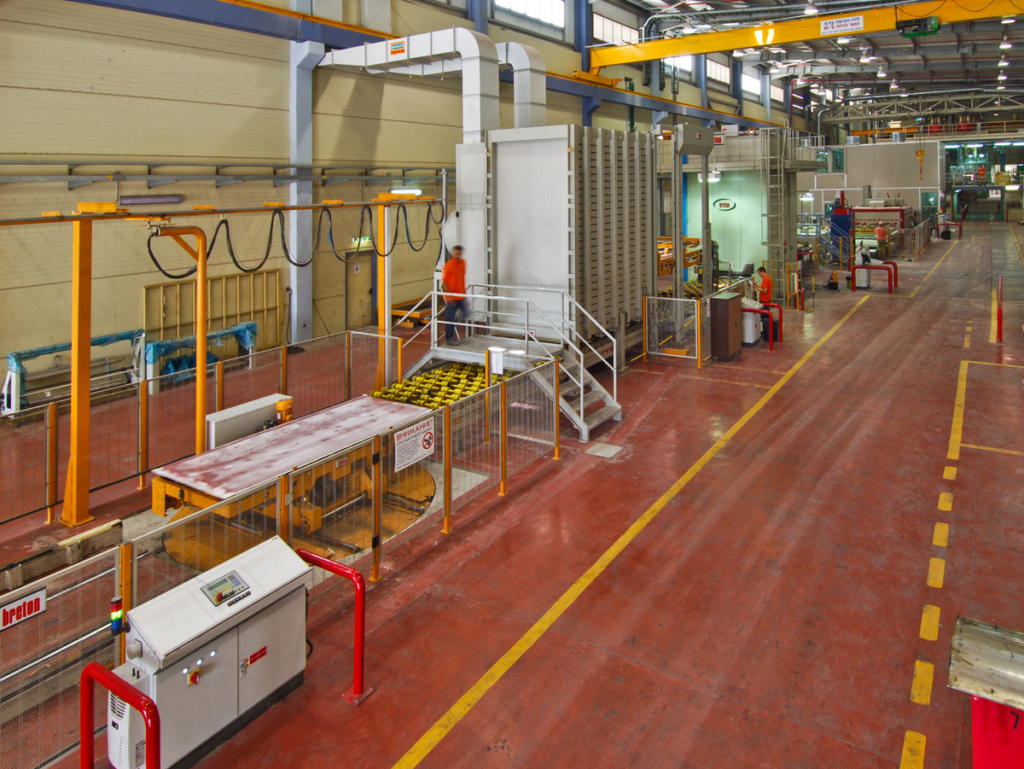
3. Curing
The slabs are then moved to the curing kiln and heated to 90°C for 45 minutes, providing the finished levels of strength and solidity.
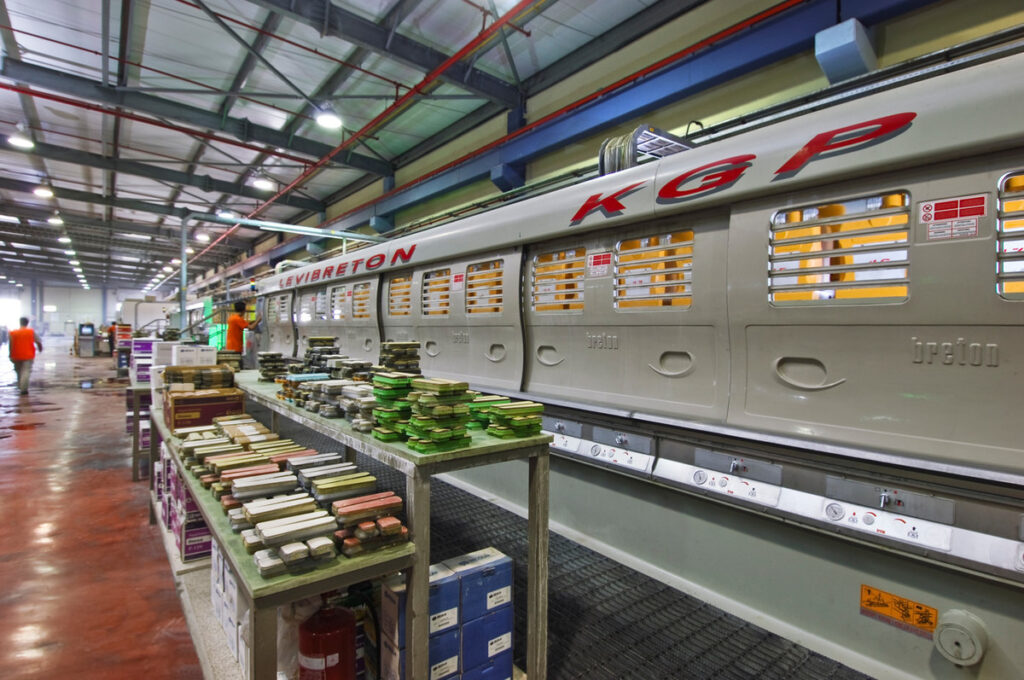
4. Polishing
The slabs are gauged, calibrated and then polished to a perfect finish in a wide range of colours and designs.

5. Quality Testing
Every slab then undergoes rigorous quality testing to ensure it meets our incredibly high standards of colour, hue, and consistency standards.

6. Tagging
The slabs are then labelled, sorted and tagged, and enter our distribution system to ensure they reach our customers in perfect condition.
Caesarstone Porcelain kitchen worktop surfaces manufacturing process
Our premium porcelain worktops are designed with state-of-the-art technology to provide maximum durability, hardness, and stain resistance.
In our innovative and advanced plant in India, porcelain surfaces are manufactured through seven main stages:
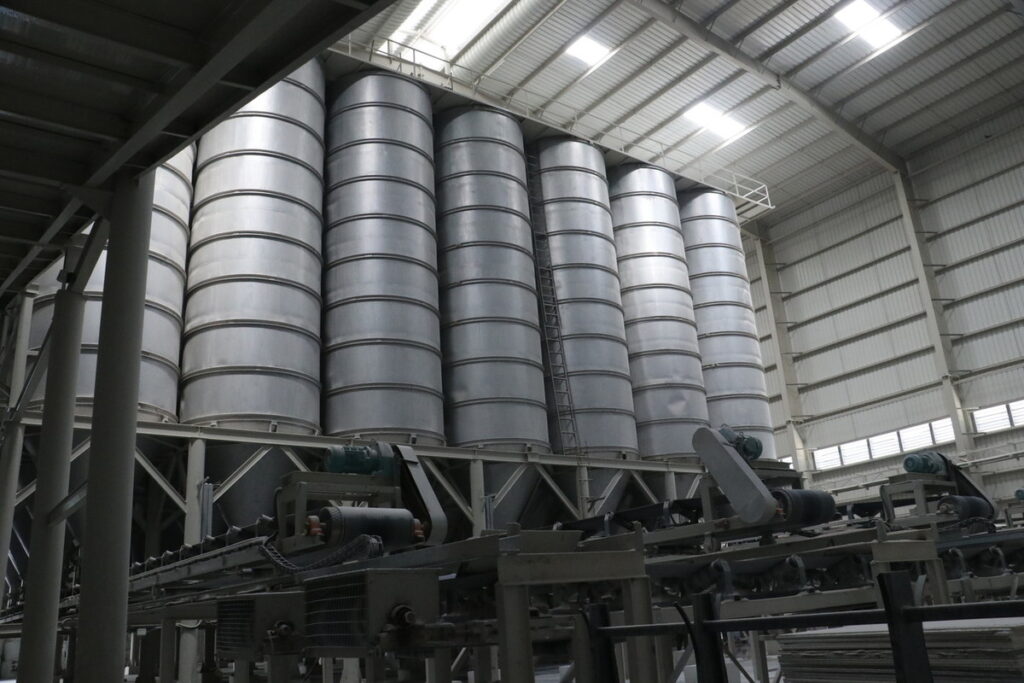
1. Preparation of raw materials
The production process begins with carefully inspecting all the raw materials that arrive at the plant. Then, the raw materials (clay and other natural minerals) are selected, tested, ground and mixed carefully and meticulously.
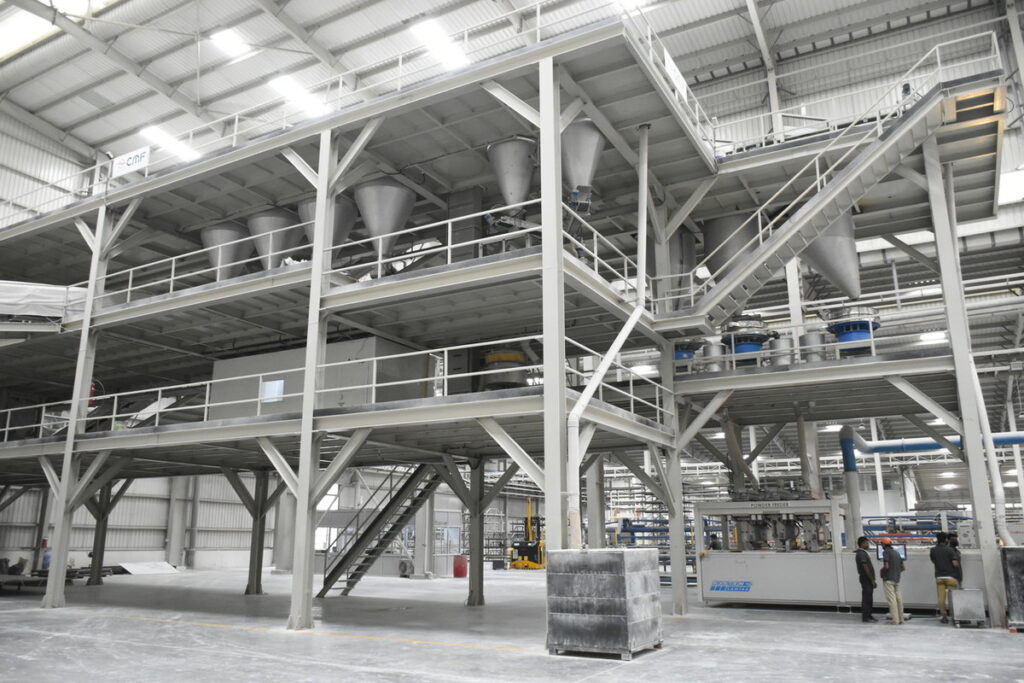
2. Compression
During the pressing process, 300 kg/cm² is applied to the mixture, ensuring the excellent properties of the surface. Afterwards, the panels are dried so there is as little humidity as possible.
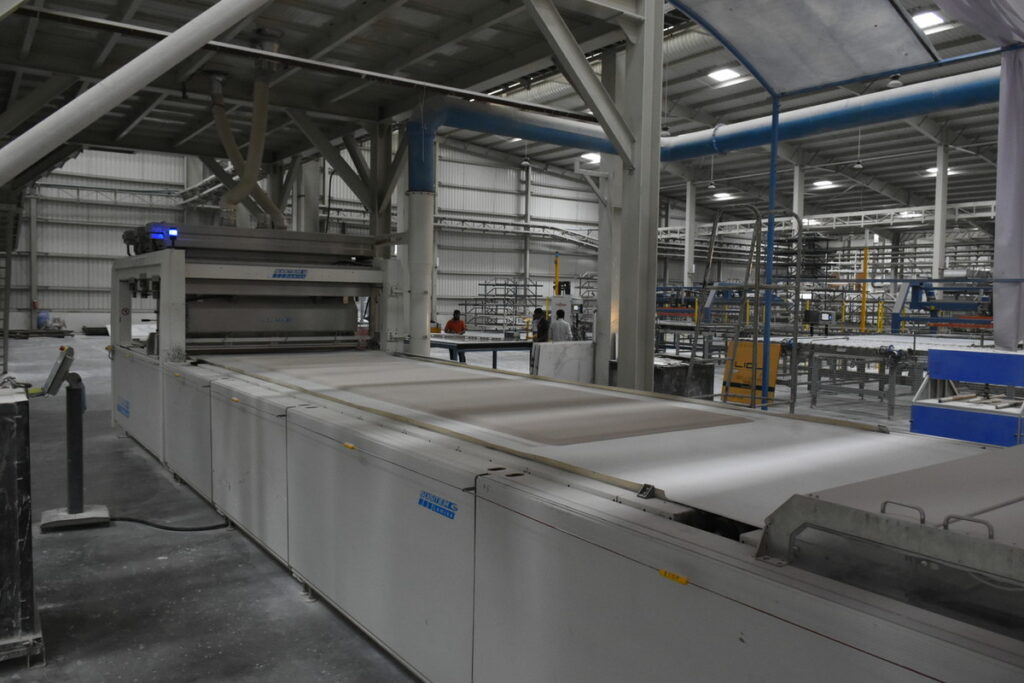
3. Digital decoration
In this stage, we create various groundbreaking colours and designs through digital printing technology and other different applicators illustrating our passion for design
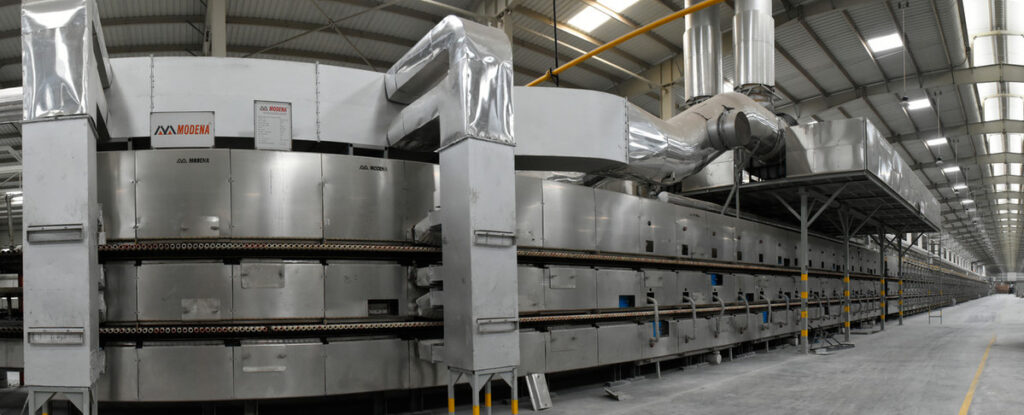
4. Firing
The porcelain slabs undergo a controlled burning process in a long and powerful kiln that reaches a temperature of 1200°. As a result, the material becomes resistant to high temperatures and heat intensities at this fusion. Furthermore, the minerals at the base of the surface are UV-resistant due to their formula.
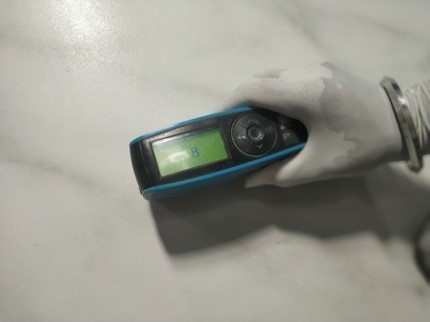
5. Polishing
The slabs are gauged, calibrated and then polished to a perfect finish in a wide range of colours and designs.
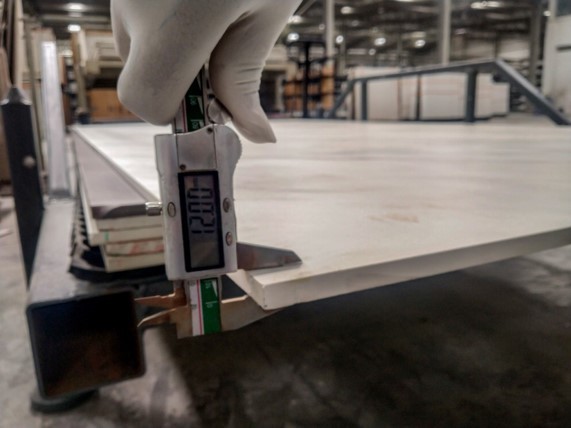
6. Quality Testing
Every slab then undergoes rigorous quality testing to ensure it meets our incredibly high standards of colour, hue, and consistency standards.
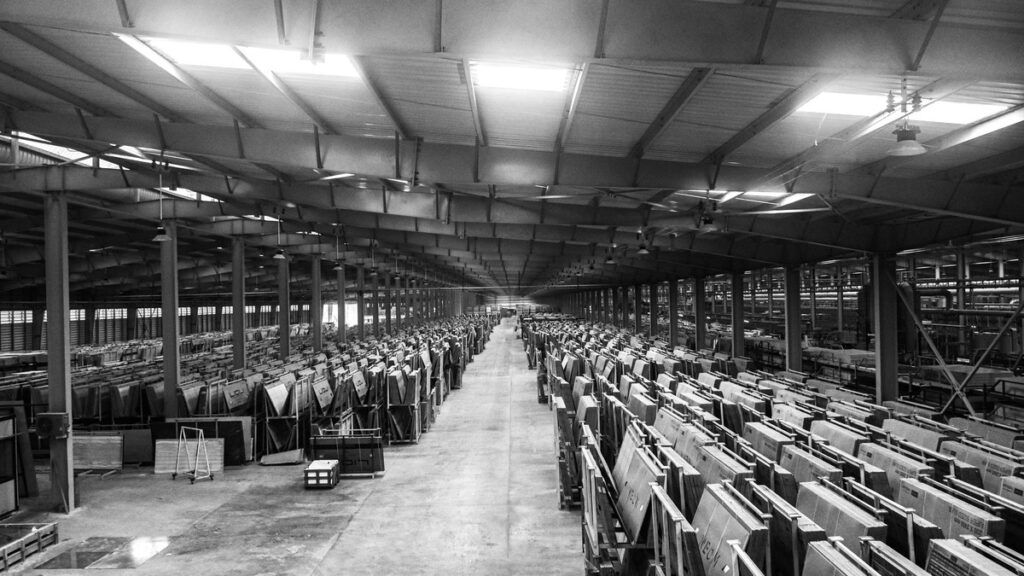
7. Packing, storage and shipping
The slabs are then labelled, sorted and tagged, and enter our distribution system to ensure they reach our customers in perfect condition.